Les structures des avions auparavant faites d’un alliage d’aluminium sont aujourd’hui tissées ! Elles utilisent ces matériaux appelés composites, car combinant des couches de fibres de carbone avec de la résine époxy. En 1988, Airbus produit le premier avion commercial avec un empennage sans métal. Cette tendance à l’abandon du métal s’est ensuite accélérée, remplacée par les composites qui constituent 53 % de l’Airbus A350.
SKF, surtout connue pour les roulements à billes, l’est beaucoup moins pour sa production de pièces aéronautiques en matériaux composite. C’est sur ce développement que Philippe Peroz président de SKF France aux côtés de ses collaborateurs présentait à la Presse une innovation dont l’entreprise Jurassienne peut s’enorgueillir.
« SKF aéronautique intègre systématiquement dans son cahier des charges, la décarbonisation. Il y a trois façons d’y parvenir : par les carburants, mais ce n’est pas notre domaine, par des moteurs plus performants, enfin par des structures moins lourdes qui vont alléger la masse des appareils ».
A volume égal, les composites sont plus légers que les métaux, même l’aluminium ou le titane. En conjuguant les diminutions des frottements et de la masse, on peut espérer une économie de 30 à 40% sur la production de CO2. Les avions volent plus longtemps en consommant moins d’énergie.
Ajoutons que la production d’une tonne d’aluminium engendre entre 9 et 12 tonnes de CO2. En minorer les besoins grâce aux composites, plus sobres et moins chers, sont autant d’avantages.
« SKF Lons-le-Saunier c’est aussi la réalisation en composite de pièces de structure »
Jusqu’alors réalisées à la main et par moulage, elles dépendaient de la disposition des fibres, donc du savoir-faire de l’opérateur.
L’idée SKF c’est d’y substituer des robots, avec dans un premier temps la réalisation des plus gros éléments comme les bielles de structure. Programmer ces robots de plusieurs tonnes pour le tissage des fibres en couches superposées impose de nombreuses adaptations pour atteindre les standards aéronautiques.
Avec la réussite de cette programmation, SKF dispose aujourd’hui d’une ligne automatisée de placement de fibres désormais fonctionnelle, qui mobilise six robots. Une réussite qui fait accéder SKF à l’industrie connectée dite « 4.0 » où à terme les machines doivent pouvoir communiquer entre elles et prendre des décisions de manière autonome.
« Nous avons aujourd’hui complétement automatisé la fabrication de ces éléments . Nous gagnons sur le poids, nous gagnons sur le coût, donc davantage de compétitivité et un bénéfice pour l’environnement. Nous allons donc à terme étendre cette automatisation ».
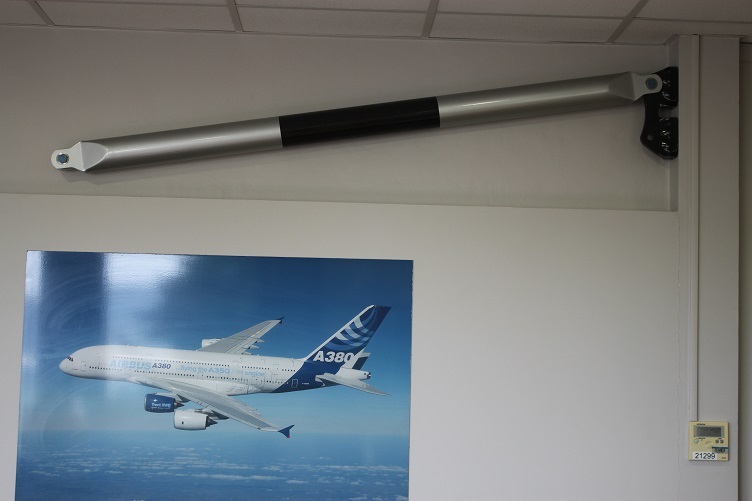
Mais que devient l’emploi ?
« La réduction des effectifs n’est plus d’actualité. Nous faisons évoluer le personnel vers ces technologies et nous venons de créer un centre de formation propre à l’entreprise. L’idée est de recruter au sortir des établissements techniques. La fibre ne doit pas faire oublier que nous produisons aussi des roulements et que nous aurons toujours besoin de tourneurs ou d’ajusteurs correctement formés. »
SKF expérimente actuellement la fibre sur d’autres sortes de pièces de structure, toujours avec la même volonté : se passer du métal, notamment le titane, très couteux et à la métallurgie difficile.
SKF Lons-le-Saunier une histoire particulière :
En 1971 SKF implante une production de roulements à billes et autres dérivés, à Lons-Le-Saunier pour profiter de l’excellence jurassienne dans les domaines de la micromécanique. Le marché est alors celui de l’automobile. En 1979 SARMA rachète l’entreprise et l’oriente vers l’aéronautique, puis en 2005, réapparition de SKF qui rachète son ancien site à SARMA. SKF conforte la vocation aéronautique de l’entreprise en ajoutant les matériaux composites à la production des roulements.